Optimizing Blown Film Line Layouts For Improved Surface Treating Performance
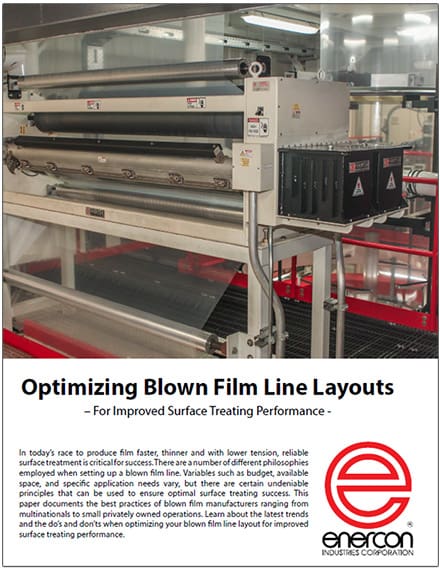
In today’s race to produce film faster, thinner and with lower tension, reliable surface treatment is critical for success. There are a number of different philosophies employed when setting up a blown film line. Variables such as budget, available space, and specific application needs vary, but there are certain undeniable principles that can be used to ensure optimal surface treating success.
This paper documents the best practices of blown film manufactures ranging from multinationals to small privately owned operations. Learn about the latest trends and the dos and don’ts when optimizing your blown film line layout for improved surface treating performance.
- Corona Treating Basics
- Roll Coverings
- Watt Density and Dyne Levels
- Alternate Treatment Technologies
- Troubleshooting Dyne Level Issues